Share





When automating for lights-out machining, a machine shop must consider everything that could go wrong well ahead of time. During a normal shift, the machine attendant can intervene when necessary, make adjustments to the setup or change out a damaged tool, then start it back up. Without the worker performing in tandem with the machine, it is vital to reduce the chance of error as much as possible.
The Schunk Tandem Vise is useful for automating robotic machining cells, including five-axis machining cells. The pneumatic or hydraulic drive enables a high degree of repeatability and consistent clamping force. Photo Credit: Schunk
An important area to consider is workholding, and Schunk VP of sales, toolholding and workholding Michael Gaunce is quite familiar with it. In working with customers, Gaunce has found that flexibility of existing Schunk workholding has meshed well with robotic automation. “When you’re loading a workpiece into the workholding with a robot, speed and simplicity are the biggest factors for success, which is why our Tandem Vise has been so successful,” he says.
Consistent Clamping
The Tandem Vise is a modular workholding system that can be operated either pneumatically or hydraulically using a wedge-hook assembly that increases rigidity. A pair of top jaws connect into the master jaws. The master jaws remain in place at the machine tool — connected to the pneumatic or hydraulic system — while the shop can switch out top jaws for different purposes. The vise comes in different sizes and strokes, with sizes ranging from 64 square mm to 315 square mm and strokes ranging from 2 mm to 15 mm.
When machining unattended, it is vital to reduce the possibility of error. By focusing on simplicity in its programming and drive, the Tandem Vise is well suited to automated applications. Photo Credit: Schunk
The vise operates independently or as part of a bundle that includes all the electrical components and valves needed for installation. To program the vise, the user inputs which valves to open for the jaws to open or close, then repeats that command whenever needed — a process designed to reduce the upfront programming. Gaunce says that the jaws will open the exact amount needed every time, delivering consistent pressure. “The simplicity of the design is really the key here,” he says. “You don’t have to worry about how the grip strength will change because it is a simple open-or-close mechanism.” The bundle also comes with a plug-in that integrates with a robot arm’s control to similarly simplify programming.
Allowing the jaws to only open or close a set amount is mean to reduce the possibility of errors creeping into the system and make it well-suited for automation. “While a ballscrew vise is more flexible,” Gaunce says, “a pneumatic vise has the repeatability of moving the same amount and applying the same force every time.” This repeatability is key to its success with automated cells.
Jaws of Vise
Of course, the Tandem Vise is not just a pneumatic jaw; it’s a modular one, too. The top jaws can be designed to hold oddly shaped parts, or standard flat jaws with or without serrations for extra gripping force. Jaws can slot in at various distances to hold parts of different sizes. The Supporting Jaw series takes this even further and uses attachable inserts that screw onto the top jaws. These inserts include soft, prismatic, pull-down and grip jaws that can be easily switched out.
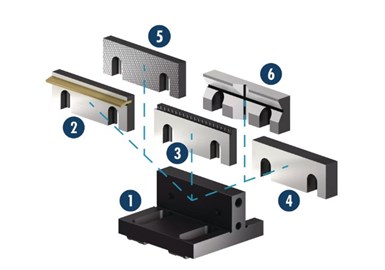
These inserts attach to the top jaw base, enabling the user to quickly change between a variety jaw types for different applications. This flexibility makes these jaws ideal for automating small-to-medium production runs. Photo Credit: Schunk
The ability to switch out top jaws makes it simple to pivot to another job once a production run is finished. The pneumatic or hydraulic action means that the shop only has to install the proper jaws at the right distance, and it is ready for the part. “We find this vise is especially effective for shops with small-to-medium production runs,” says Gaunce. “The master jaws can remain installed in the machine tool for multiple robot-assisted production runs of 20-300 parts over the course of a month.”
Part of technological progress is finding the ways established technologies and newer technologies mesh together to improve manufacturing. While some of the individual capabilities within this system are not new, it is the benefits that integrated systems can provide to automated machining cells that are becoming more important to today’s job shops.
Related Content
Quick-Change Tool Heads Reduce Setup on Swiss-Type Turning Centers
This new quick-change tooling system enables shops to get more production from their Swiss turning centers through reduced tool setup time and matches the performance of a solid tool.
Read MoreHow to Troubleshoot Issues With Tool Life
Diagnosing when a tool is failing is important because it sets an expectation and a benchmark for improvements. Finding out why gives us a clue for how to fix it.
Read MoreChuck Jaws Achieve 77% Weight Reduction Through 3D Printing
Alpha Precision Group (APG) has developed an innovative workholding design for faster spindle speeds through sinter-based additive manufacturing.
Read MoreShop Reclaims 10,000 Square Feet with Inventory Management System
Intech Athens’ inventory management system, which includes vertical lift modules from Kardex Remstar and tool management software from ZOLLER, has saved the company time, space and money.
Read MoreRead Next
AMRs Are Moving Into Manufacturing: 4 Considerations for Implementation
AMRs can provide a flexible, easy-to-use automation platform so long as manufacturers choose a suitable task and prepare their facilities.
Read MoreMachine Shop MBA
Making Chips and Modern Machine Shop are teaming up for a new podcast series called Machine Shop MBA—designed to help manufacturers measure their success against the industry’s best. Through the lens of the Top Shops benchmarking program, the series explores the KPIs that set high-performing shops apart, from machine utilization and first-pass yield to employee engagement and revenue per employee.
Read More